How digital is mitigating ongoing supply chain disruption
Accelerating growth: How digitalisation is reshaping global supply chains
- The global supply chain has been through mass changes in recent years in response to the COVID-19 pandemic and other challenges. In this new article, Sedna’s logistics expert, Warren Kucker, explores how digital tools can help the sector evolve the daily working patterns and use this time to accelerate growth.
Global markets are almost unrecognisable compared to the past two years, which saw unprecedented disruption and growth in equal measure. But while supply-chain strains are (for the most part) easing, things are far from back to ‘normal’. According to Forbes, February 2023 marked the thirty-fifth month of disruption higher than at the end of the 2007 recession – a level of chaos that would previously have been unthinkable.
In the last few years alone, there have been repercussions not only from the devastating COVID-19 pandemic, but also raw material shortages, extreme weather events, international port backups, intermittent factory closures, product shortages, rail disruptions, skyrocketing inflation and major geopolitical events such as the Russo-Ukrainian war. The implications of these have combined to form major ongoing challenges, testing the resilience and adaptability of modern supply chains across industries.
But despite these significant disruptions, 92% of supply chain leaders did not halt technology investment during the pandemic, speaking to the value of a digital supply chain in helping enterprises navigate disruption and mitigate risk.
To compete in this new world, supply chains need to be automated, high speed and efficient. But until recently, the technology to support this has been siloed, expensive and slow to implement. Now, smarter tools are available to provide businesses with greater control over their supply chains. Resilient supply chains, enabled by this new technology, can be a strategic differentiator, a competitive necessity and an engine for growth.
Below I outline some of the main, overlapping factors putting ongoing pressure on businesses across the world, followed by some of the technological innovations helping companies to turn vulnerabilities into strengths.
The fallout from the pandemic
The pandemic disrupted global economies to an extent rarely seen over the past century. During the 2020 lockdowns, crew illnesses from the virus and increased consumer spending placed the container supply chain under unprecedented strain, overwhelming ports and distribution centres, with disruption causing not just days, but weeks of delays. It also caused carrier profits to soar. It’s unsurprising, then, that research by Ernst & Young found that 72% of supply chain companies surveyed saw a negative effect from the pandemic.
Following on from China ending its own lockdowns and reopening trade, shipping leaders are watching carefully to see if the boost in global consumption and demand will reduce or increase strain in value chains.
A receding global economy
The global economy is proving resilient in early 2023; last month, for a fourth consecutive month, the S&P Global Market Intelligence forecast of 2023 global economic growth was revised upwards. In fact, S&P predicts world real GDP growth to pick up from 2.0% in 2023 to 2.9% in 2024.
However, while rising prices are helping to offset higher expenses, price increases also leave consumers struggling to buy essentials such as food, clothing and medical care.
With less disposable income, there is shrinking demand for some goods and services.With supply conditions improving, progress in reducing inflation will continue. But even if inflation eases, prices are likely to remain high compared to pre-pandemic levels.
The impact of the Russo-Ukraine war
The 2022 invasion of Ukraine by Russia caused several price spikes and both the ongoing war and global sanctions continue to disrupt the flow of critical commodities, as well as to pose a threat to cybersecurity.
While it might be tempting to label this as solely affecting the European region, the impact of the Russo-Ukraine war stretches beyond a single continent. Ukraine and Russia are in the top three producers in the world for a number of key resources – especially within agricultural production, like wheat, corn, barley and sunflower oil – and the conflict has forced countries around the world to source food, raw materials, fossil fuels and more from new trading partners. This has impacted countries without the buying power to shift to higher-cost sources.
What’s more, 14.5% of all seafarers are either Russian or Ukrainian people. This could further impact diminishing labor availability for ocean freight providers.
Labour disputes
The ongoing threat of US labour strikes could bring major routes for freight shipping to a halt. 2022 saw railroad workers and unions putting pressure on US Congress to improve working conditions, threatening to strike in September in a move that would have cost the US economy an estimated $2bn a day.
West Coast dockworkers have been working without a contract in place since last autumn (the International Longshore & Warehouse Union (ILWU) and the Pacific Maritime Association (PMA) are still in negotiations). Meanwhile, UPS workers have emphasized they will strike this summer if a new contract agreement isn’t reached on time. And worker unrest isn’t limited to the United States; over the past year there have been similar strikes in major ports in countries including the UK, Germany, and South Africa.
Climate crisis
On top of political unrest and economic upheaval, there is another, increasingly serious threat to supply chains: the climate crisis. Extreme weather, from hurricanes to floods to wildfires, is on the rise, causing disruption both locally and across the world from where the specific event is taking place. Examples from February 2021 alone include heavy rainfall causing the banks of the Rhine River to burst, holding up Europe’s most important commercial waterway for several days, and the Texas freeze, which caused the worst involuntary blackout in US history, forcing three major semiconductor plants to close.
Scientists predict these events will only grow in intensity and regularity – and that’s before factoring in the impending threat of sea level rise, which is likely to affect ports, rail lines, highways and other supply infrastructure.
How technology is enhancing collaboration and reducing risk
Resilience takes the right mix of operations and logistics capabilities, and greater visibility across the supply chain, to support a diversified customer and supplier base while avoiding fragmentation. The right technology doesn’t just free up time, energy and resources. It also increases transparency, allows access to data that can provide valuable insights, and can advance your business’ ability to plan for and mitigate market volatility.
On top of this, technology – alongside proper training – can reduce pressure on employees and reduce the risk of fallout, particularly when teams are empowered to own and utilise these platforms in their day-to-day. Rather than falling back on low-cost labour and lean operations, resilient supply chains of the future will rely on agility, automation, visibility and upskilling, leading to informed decision-making, increased security and standardisation.
Of course, it’s not as simple as signing up for a ton of new software. To create a digitised, autonomous supply chain you need connected technologies across each link in the chain – planning, procurement, manufacturing and logistics.
Gathering better quality data across the supply chain
Many operators are still making decisions based on limited data sets, attempting to mitigate significant risks based on past experience. Supply chain leaders need better data to increase real-time visibility and monitoring of the end-to-end supply chain, assess carrier performance, and aid scenario planning. It needs to be standardised and translated in a way that is relevant for all parties across the chain.
The demand for transparency across hundreds, or even thousands, of suppliers is causing a shift from linear supply chains to decentralized, integrated networks, enabled by Internet of Things (IoT) sensors. These sensors provide real-time data on where goods are in the chain and, when relevant, can even share updates on their condition (such as whether they are being kept at the correct temperature). IoT devices are compatible with modern enterprise resource planning (ERP) systems and the data they provide allows companies to allocate product and inventory more efficiently.
Breaking down data silos
Gathering more data can only take you so far if it remains stuck in silos. The more data a company gathers, the bigger the danger of creating bottlenecks when it comes to analysing and utilising it for decision-making.
With many companies now working with ten times the number of suppliers they were pre-pandemic, relying on on-site, decades-old electronic data interchange (EDI)-based systems makes it that much harder to be competitive in a lower-margin landscape where speed and automation are differentiators. Rather than sticking to old data transmission technologies, shifting information into a cloud-based server increases collaboration and data-sharing among suppliers and enables real-time decision-making.
Cloud-based platforms help to bridge data silos by integrating and hosting other applications for a better user experience. By feeding information back into the supply chain management process, you can drive improvements across the board.
Creating an end-to-end picture of the supply chain
Companies can only manage their supply chains effectively when they have a clear picture of each link. According to Forbes, during the pandemic, 94% of supply chain decisions were based on spreadsheet analysis – but a spreadsheet can’t adequately monitor and model supply chain complexity. Network design simulation technologies can factor the impact of demand and supply variability into a complete cost analysis. Some platforms also allow you to track consumer sentiment via demand-sensing signals to influence production.
Speeding up decision-making and spotting risks
Predictive analytics tools can be layered over existing risk management systems to spot trends, patterns and potential disruptions within supply chains, and to help identify the right risk mitigation strategies. By predicting surges or slowdowns, these tools can also help manage financial risks and vulnerabilities. IoT sensors can also come into play here by acting as digital twins, allowing companies to understand risk exposure and run disruption simulations. By feeding real-time data from these sensors into digital models of their supply chains, companies can test hypothetical responses to disruptive scenarios, monitoring their impact.
AI, too, has a central role to play in the future of supply chains. While the technology is only in its infancy, we’re only scratching the surface of its capabilities. At present, 37% of supply chain leaders are already deploying AI and machine learning, while another 36% are planning to use them soon. What’s more, by 2035, 45% of supply chains are expected to be mostly autonomous, enabled by robots in warehouses and stores, driverless forklifts and trucks, delivery drones and fully-automated planning.
As the maritime industry works towards producing standardised data sets, AI is likely to be used in the not-too-distant future to predict spikes in demand, disruption or even delays affecting specific vessels. It could also be used to standardise information across different tech platforms, suppliers and regions, creating a smooth data flow without the need for a monolithic system.
Shifting towards smarter comms
With a just-in-time inventory approach becoming the norm, companies are expected to provide rapid, real-time updates on the location of specific products, all while working with a vast number of vendors. Tech-enabled comms tools can support your teams in navigating an increasingly competitive, fast-moving market.
On-site (also known as on-prem) ERP systems are restricted in how they can talk to each other and expensive to upgrade, with data often shared in spreadsheets and via email along the way. By shifting away from EDI towards application programming interface (API), technologies will allow company to communicate in real-time with manufacturers across the world and encrypt sensitive data for increased security.
If you are sharing data via email, then clear, fast and secure communication is vital. 60% of emails received are irrelevant but missing important emails carries heavy – often financial – consequences, and the mishandling of personal data risks massive penalties. Intelligent email platforms connect your email to your core business systems, like SEDNA, organise messages automatically and can use AI to protect sensitive and confidential data, like Personal Identifiable Information, which can otherwise require manual effort.
Looking forward, the next step for messaging and data sharing systems will be enabling users to open an encrypted, verified security channel between a sender and a recipient, avoiding the risk of security systems mistakenly blocking useful qualitative data.
Investing in an intelligent future
Times of crises don’t have to lead to disaster. In fact, there are numerous examples of individuals, companies and countries emerging from periods of severe disruption into a growth trajectory (think the 1918 flu pandemic followed by the ‘Roaring 20s’).
Ultimately, we have to think about how to avoid the next big global crisis, whatever it may be. The scars of COVID-19 will overhang for quite some time. However, through our direct, personal, and global experience of the fragility and vulnerability of supply chains – and the power of technology in mitigating such impact – we can push forward the digitisation age in supply chain operations.
Innovation tends to go hand-in-hand with crisis and is critical to a strong recovery. With many business leaders already investing strategically in next-generation technology to remain flexible, adaptable and on top of future challenges, supply chain digitisation is well and truly underway.
Latest resources
Driving faster action and insights from your core business system
Connected Apps integrate business-critical data hidden across your digital ecosystem. Make informed decisions without needing to switch contexts or systems.
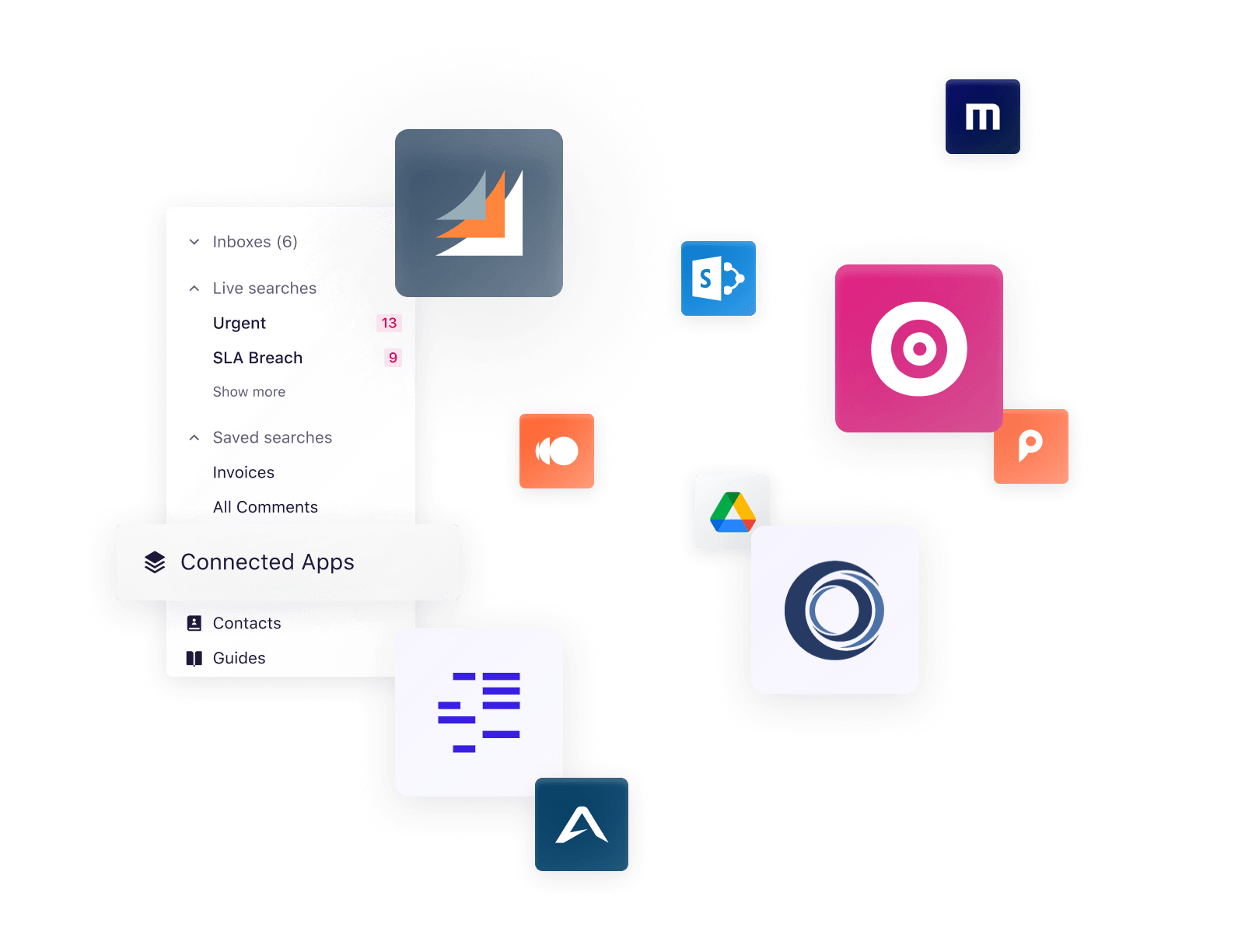